3D selective paint removal
The solution introduces 3D selective paint layer removal
Application: Laser decoatig
Industry: Automotive
Task
Manufacturers of aluminum wheels face increasing demands for design. There is a growing emphasis on attractive patterns and color combinations. However, designers often encounter technological limitations and complexities in production. For instance, traditional CNC machining is time-consuming and unsuitable for all surface types. Additionally, newly proposed design solutions can be cost-intensive.
LASCAM systems has therefore introduced an advanced solution to push these boundaries – laser-based 3D selective removal of painted layers, which enables quick, precise, and design-unrestricted customization of aluminum wheels.
How It Works
The laser removes only the top colored layer in a range of 20–35 μm, without damaging the underlying protective coating on the alloy. A hard clear acrylic coating is then applied to protect the design from environmental effects. This allows for detailed patterns to be applied to wheels without the need for CNC milling.
Different colors require individualized process parameters – metallic shades (such as blue or silver) demand high precision to avoid damage.
Solutions
Unlike conventional lasers with 10–200 W output, this solution uses a high average laser power ranging from
several hundred watts to a few kilowatts, allowing for fast and efficient processing of larger areas while maintaining the required quality.
Outcome:
- wide field of view up to 600 × 600 × 60 mm with minimal spatial deviation at the edges,
- sharp laser spot (approx. 1 mm) at optimal focus distance,
- automatic recognition camera using neural networks that optically identifies wheel type and position, increasing the system’s functionality and flexibility.
Integration into Fully Automated Production
The technology can be integrated as a fully automated in-line solution within the production line for cast wheels. The wheel is transported on a conveyor and then securely fixed under a camera system. The camera identifies the wheel type and records its exact position. Based on this, the system generates a 3D laser trajectory tailored specifically for the part. The process laser head interprets these instructions and performs the required task using a high-power cleaning laser.
The results show significant acceleration in production, elimination of manual masking, and overall process
simplification.
The installation also includes ionized air blowing, advanced fume extraction, and optical result inspection – all tailored to the specific requirements of the customer’s wheel manufacturing operation.
Key benefits
- Paint removal without damaging the base layer of coating that protects the wheel alloy.
- Nearly unlimited range of patterns and designs.
- Elimination of production steps (surface milling, need to mask screw holes and hub contact areas before painting, complex programming).
- Cost savings by eliminating redundant steps in the production process.
- Reduced energy consumption and contribution to CO2 neutrality.

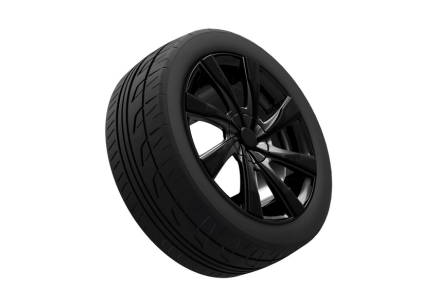